Design and control future-proof processes with Pexcite software solutions
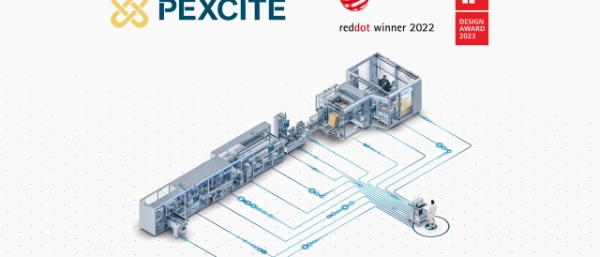
Pharmaceutical and biotech companies face many complex new regulatory requirements. Especially sustainability which has become increasingly important. Many process-relevant resources are in question. In addition, there are uncertainties in the supply chains and staff shortages. Processes have to be changed, restructured and, above all, made more efficient. As a result, digitalization plays a decisive role here: because only detailed information and data enable those responsible to initiate the right measures for optimizing processes and improving overall equipment effectiveness (OEE). With Pexcite, Uhlmann Pac-Systeme presents a modular software solution that can be used to plan, control and monitor production, packaging and logistics processes in the pharmaceutical and biotech industry: for greater efficiency and longer machine and plant runtimes.
Use and manage all data in the value chain
Pexcite solutions network individual machines, lines or entire plants across all interfaces, store process-relevant data and parameters and thus create transparency. This enables centralized control of the processes. Depending on their needs, users can choose to use individual functions or combine several. Even with the basic version of Pexcite, users cover the essential requirements for digital data management in a regulated pharmaceutical environment. The software can be used to centrally monitor and control individual lines up to an entire plant. Batch management, audit trails, the management of alarms as well as central reporting are part of the range of functions and are configured specifically for each user. Pexcite is manufacturer-independent and can process all common machine and data interfaces.
Easily adapt Pexcite to the customer-specific business process
Once installed, Pexcite can be expanded with further pharma-specific software modules from Uhlmann Pac-Systeme. One widely used module is Track & Trace, which enables companies to meet global product safety requirements and other regulatory obligations. Digital Tool Management makes it much easier to manage and supply format parts and to plan the corresponding set-up times. Pexcite Supervisory Control facilitates centralized management of product and format data via interfaces to ERP and MES, and distribution to connected machines from a wide range of manufacturers at the touch of a button. Previously, this order-specific batch data, product master data and machine formats had to be entered separately for each machine. Pexcite Supervisory Control significantly reduces process complexity and improves reliability. The overall plant efficiency is thus significantly improved. With Smart Monitoring in Pexcite, key parameters such as OEE or energy and resource consumption are consistently visualized and monitored. The live dashboard provides detailed insights into the overall plant efficiency of all machines on the line – divided into the three main components of availability, performance and quality.
Detailed access rights management and individually configured dashboards
In order for users to be able to work meaningfully with the flood of data and information Pexcite provides, the development team places special emphasis on the design of the user interface and also the possibility to create different user groups. After all, someone who works directly on a line needs different data, control and monitoring functions than someone who is responsible for the overall process or the person who manages spare parts and consumables. Pexcite has a central user administration with Active Directory to provide extensive configuration options and reliable mechanisms to authenticate users and grant access rights. Pexcite is web-based: User groups can access the system directly at the machine, via mobile devices or stationary in the office, and all data is always live. The Pexcite user interface is designed as a dashboard and can be individually configured by the users. Numerous widgets and shortcuts are available for this purpose. For example, alarms, the production status of various machines or overviews of the entire line can be configured according to individual requirements.