Blow-Fill-Seal-Ampullen: exakt etikettiert, effizient verpackt
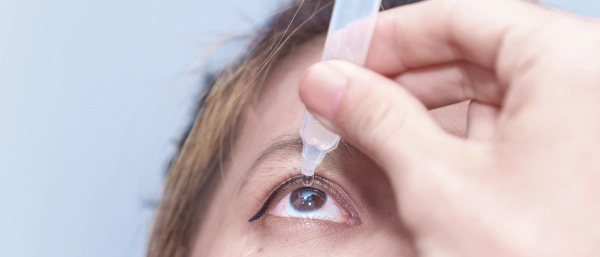
Wenn die Anforderungen so ungewöhnlich sind, dass keine Standardmaschinen sie abdecken können, dann schlägt die Stunde von Uhlmann. Unter Leitung von Projektmanagerin Janina Triska entwickelte ein Technikteam eine höchst komplexe Verpackungslinie für Blow-Fill-Seal-Ampullen: Fünf Einzelmaschinen von drei Herstellern sollten in eine Linie integriert werden. Hier war Know-how und Kreativität gefragt!
Der Auftrag: Blow-Fill-Seal-Ampullen beidseitig zu etikettieren und zu verpacken
„Schon ganz am Anfang war klar: diese Linie wird nicht Standard“, erinnert sich Janina Triska. Die 33-Jährige Wirtschaftsingenieurin ist als Projektmanagerin bei Uhlmann für hochindividualisierte Pharma-Packaging-Linien zuständig.
Die Angebotsphase
Gemeinsam mit ihrem Kollegen, dem Sales Manager Christian Rotter, entschied sie, bereits in der Angebotsphase in das Projekt einzusteigen. Rückblickend ist sie froh über diesen Schritt: „Erstens hatte der Kunde sofort einen positiven Eindruck davon, wie wir arbeiten. Und zweitens konnten wir uns persönlich kennenlernen.“
Die Linie
Es war der erste und letzte persönliche Termin, denn kurz danach begann der erste Lockdown und das Team arbeitete remote weiter. Eine enge Abstimmung war notwendig, denn die Linie hatte es in sich: Der Auftrag lautete, Blow-Fill-Seal-Ampullen beidseitig zu etikettieren und zu verpacken:
- Von der kontinuierlich produzierenden Blow-Fill-Seal-Anlage liefen die Ampullen in einen großen Speicher und danach wurde die Dichtigkeit geprüft.
- Über ein Förderband sollten die Ampullen dann als Fünferstreifen zum Etikettierer gelangen und dort beidseitig etikettiert werden. Zwei Drucker galt es zu integrieren, davon würde einer die Labels mit dem Verfallsdatum inline bedrucken.
- Danach war der Anschluss einer Schlauchbeutelmaschine geplant. Das Verfallsdatum sollte zusätzlich mit einem Lasermarkiersystem auf die Schlauchbeutel aufgebracht werden.
- Auf einem Zwischenband sollten die Beutel zum Uhlmann-Kartonierer C 2155 transportiert und in fünf verschiedenen Packungsgrößen in Faltschachteln verpackt werden.
- Am Ende waren eine Waage sowie ein Casepacker für die Verpackung in Versandkartons vorgesehen.
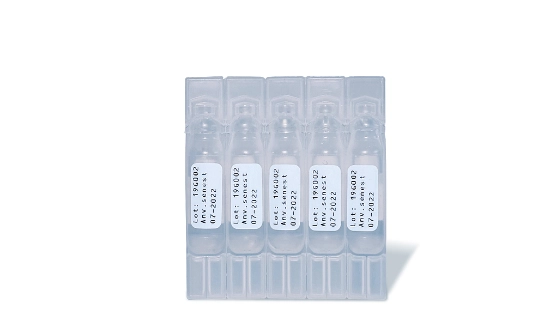
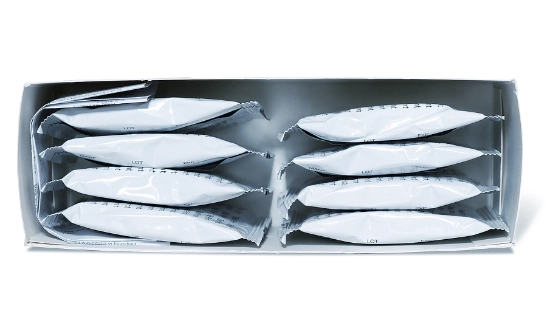
Die Aufgabe: fünf Einzelmaschinen von drei Herstellern in eine Linie zu integrieren
Die Herausforderungen und wie das Team sie gelöst hat
1. Integration in eine Linie
Damit alles optimal zusammenspielt, hatte der Kunde nicht nur das Projektmanagement an Uhlmann übergeben, sondern auch die Schnittstellenanbindung. Bei jeder Maschine wurde die Schnittstelle zur vor- und nachgeschalteten Maschine detailliert geklärt.
2. Präzise Etikettierung auf beiden Seiten
Die zweite Herausforderung wartete im Etikettierprozess auf das Team: Die Blow-Fill-Seal-Ampullen sollten beidseitig etikettiert werden, wobei der Kunde besonderen Wert auf die exakte Positionierung der Labels legte. Der Fünferstreifen aus Kunststoffampullen war jedoch flexibel, was das Drehen und Etikettieren erschwerte.
Hier arbeitete das Team mit Erfahrungen aus früheren Projekten, dem 3D-Model und Tests an der Maschine um die optimale Lösung zu entwickeln. Die Etiketten werden einseitig aufgebracht, über ein Kamerasystem kontrolliert und gegebenenfalls ausgeschleust. Über eine eigens entwickelte Führung werden die Ampullen um 180 Grad gedreht, ausgerichtet und auf der zweiten Seite etikettiert. Eine weitere Kamera stellt sicher, dass nur einwandfreie Produkte zum Folgeprozess gelangen. Am Ende setzt ein Roboter die Ampullen auf das Transportband der Schlauchbeutelmaschine über.
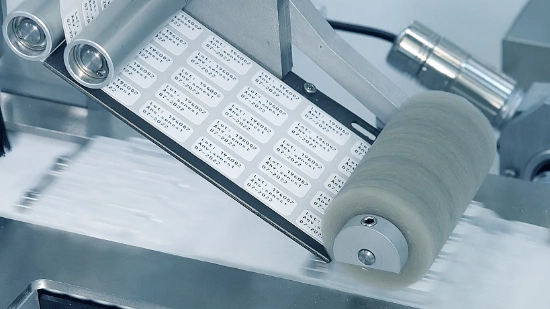
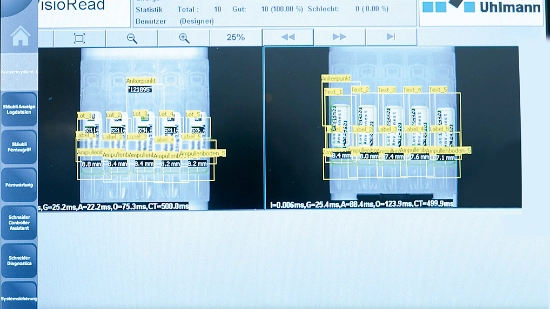
Stabiler Prozess durch Simulation und Tests
3. Sichere Einbindung eines Lasers
In der Schlauchbeutelmaschine galt es, einen Laser für die Markierung des Schlauchbeutels mit dem Verfallsdatum einzubinden. Das war technisch keine Herausforderung – aber organisatorisch. Das Projektteam bezog die Laserbeauftragten bei Uhlmann mit ein und entwickelte Maßnahmen, um sowohl für die Montage und die Tests als auch für die spätere Nutzung maximale Sicherheit zu erreichen.
4. Kartonierung von zwei instabilen Stapeln
Ein Stapel aus Schlauchbeuteln kommt schnell ins Rutschen – das musste auch das Uhlmann-Team feststellen, als es den Kartonierer konfigurierte. Insgesamt plante der Kunde fünf Packungsgrößen – von zwei Packungen pro Faltschachtel bis zu zwei Stapel à sechs Packungen. „Wir sind mit einer detaillierten Risikoanalyse gestartet und haben verschiedene Lösungen konzipiert, die wir anschließend digital simuliert haben. Bereits seit 2015 arbeiten wir mit der Technik eines digitalen Zwillings. Dabei entwickeln wir die komplette Linie am PC und testen sie in Form einer Computersimulation. Dabei verbinden wir durch die „Hardware in the Loop“ Methode die Mechanik der Maschine mit der Steuerungstechnik. So sind wir sicher, dass alles funktioniert, noch bevor die erste Bodenplatte in der Montagehalle steht“, erklärt Janina Triska.
Auf diese Weise konnte das Team einen Gegenhalter entwickeln, welcher die Stapel sowohl vor als auch während des Einschiebens in die Faltschachtel stabil hält. Und das war auch notwendig, denn bei den größeren Einheiten wurde zuerst ein Stapel gebildet und geparkt. War der zweite Stapel fertig, wurden beide nacheinander in die Faltschachtel eingeschoben. Für diesen Prozess war ein getakteter Kartonierer erforderlich, mit einer Besonderheit: die Packgutkette musste doppelt so schnell laufen wie die Faltschachtelkette. Dank der guten Zusammenarbeit von Konstruktion, Technik und Programmierung konnte das Team einen stabilen, sicheren Prozess gewährleisten.
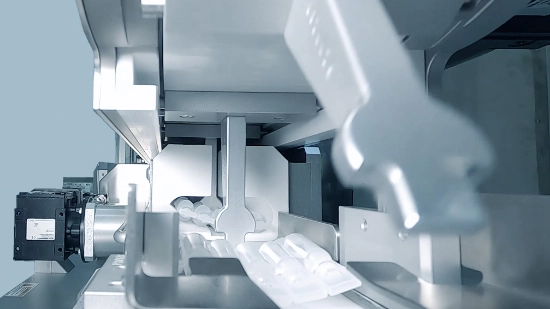
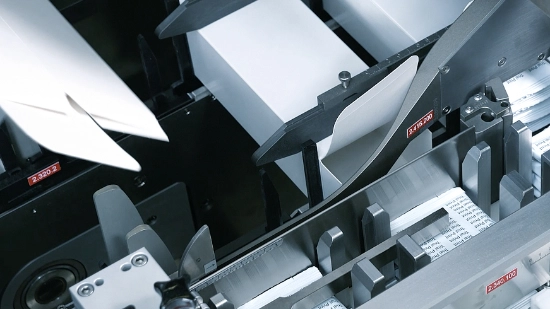
Das Ergebnis
Mit täglichen Online-Meetings, engen Abstimmungsschleifen und einer hervorragenden Zusammenarbeit untereinander, aber auch mit den Kunden und Zulieferern, konnte die Linie fertiggestellt und ein Factory Acceptance Test remote durchgeführt werden. Mittlerweile ist die Linie ausgeliefert. Die erste Testproduktion lief einwandfrei. „Es lief alles reibungslos. Der Kunde war sehr zufrieden mit der Linie, dem Projektmanagement und der guten Zusammenarbeit – und wir als Projektteam auch. Alle waren stolz ein exzellentes Ergebnis erreicht zu haben“, so Janina Triska.
Fragt man sie nach dem entscheidenden Erfolgsfaktor, muss sie nicht lange nachdenken: „Das Team! Wir haben bewusst mit einer kleinen, interdisziplinären Gruppe von Spezialist:innen gearbeitet – jeweils nur ein Monteur, ein Konstrukteur und ein Programmierer pro Maschine. Das hat hervorragend funktioniert. Deshalb geht ein großes Dankeschön an meine Kolleginnen und Kollegen!“
„Bereits seit 2015 arbeiten wir mit der Technik eines digitalen Zwillings. Dabei entwickeln wir die komplette Linie am PC und testen sie in Form einer Computersimulation. So sind wir sicher, dass alles funktioniert, noch bevor die erste Bodenplatte in der Montagehalle steht.‟
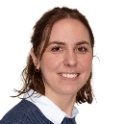
Janina Triska
Projektmanagerin