Always one step ahead
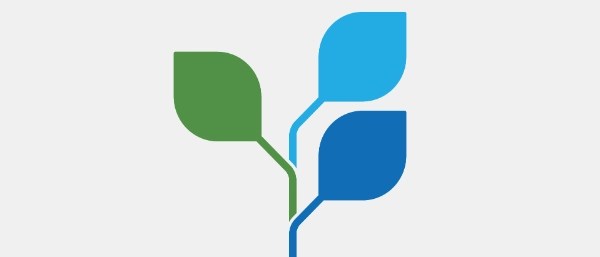
For many years, multi-material packaging was hard to beat when it came to most of the parameters important to pharmaceutical packaging: costs, process reliability and user-friendliness. But priorities are changing massively and sustainable packaging is also becoming a must in the pharmaceutical industry. Uhlmann Pac-Systeme is ahead of the game and able to offer innovative solutions that will allow packers to position themselves for the future.
Long more of a buzzword than a strategic goal, the role of sustainability in the pharmaceutical packaging industry is currently undergoing fundamental change. In the EU, being able to prove the existence of a sustainability strategy accompanied by decarbonization targets and evidence of its implementation is becoming a legal obligation for many companies. In an increasing number of markets, the production of plastic waste is also already subject to specific financial sanctions, e.g. through corresponding taxes or recycling requirements. Alongside this, however, many companies have also set themsleves ambitious sustainability targets: out of a sense of responsibility for the future of the company and the common environment.
In the area of packaging for pharmaceutical products, especially medicines, the switch to sustainable or largely plastic-free packaging poses a major challenge. After all, especially in the area of sensitive medications, there are fundamental functional and technical reasons why multi-substance packaging options are the first choice. They often allow requirements for the protection of active ingredients to be ensured both more reliably and less expensively than is possible with pure paper or cardboard-based packaging.
Furthermore, there is another obstacle to the changeover. In many cases, the primary and secondary packaging of a drug forms an integral part of the required approval. Changes to the packaging and in the packaging process have to go through an elaborate, cost-intensive approval process.
Paper-based packaging has the image of being particularly sustainable – especially among end consumers, and it is certainly true that paper has a high recycling factor. However, in other key aspects upon which the real sustainability of a packaging solution depends, paper and cardboard do not necessarily perform better than some plastics. For example, water and land consumption and the use of bleaching agents and other chemicals in the production of paper and cardboard are decisive factors in any assessment of their sustainability. Moreover, forestry plantations are often huge monocultures and ecological deserts with poor living conditions for workers. Only paper that is certified by reputable agencies as comprehensively sustainable really contributes to the positive climate and ecobalance of a packaging solution.
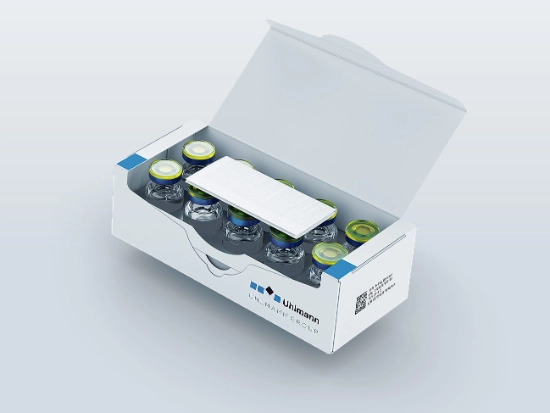
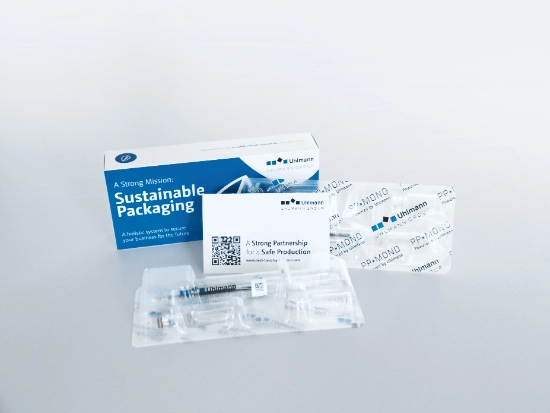
However, sourcing is not the only limiting factor for paper. Until now, pure paper-based packaging has usually only been technically possible as secondary packaging, e.g. as cartons or trays. At Uhlmann, we are currently working intensively with film and paper manufacturers on solutions, such as paper blisters, which will also protect sensitive products from external influences such as water vapor and ensure process reliability. Some of these are already ready for the market, and further alternatives will certainly be added in the next few years. For example, highly sensitive parenteral products can be safely packaged in paper or plastic trays on our PTC 200 cartoning line, with the high degree of modularity of the individual system components making this changeover possible.
Plastics now offer a wide range of possibilities for combining very good barrier properties and process reliability with high sustainability value. The magic word here is mono-materials. Packaging solutions made from one type of plastic are highly recyclable and thus have a good sustainability profile. Here we offer process-safe solutions for both solids and parenteral products. For example, the Blister machine BLU 200 is also available as a version for the efficient, safe processing of PP mono film. The BEC Blister line is perfectly suited to the packaging of solid dose products in PP mono blisters or other sustainable packaging materials. Further solutions are in the pipeline and will be launched in the near future.
“Different materials, different process behavior, new packaging design – the switch to sustainable packaging solutions is a complex process. At Uhlmann, we are already greatly experienced in this and can support you in all areas: from material selection to process optimization.”
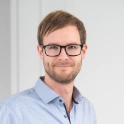
Valentin Knupfer
Team Leader Process Automation & Optimization
Making packaging processes more sustainable usually requires changes to proven set-ups. Our sustainability experts already have a great deal of experience in this area. Contact us and we will be happy to advise you on how to improve your packaging processes in a sustainable and therefore future-proof manner. For the changeover from PVC aluminum blisters to mono-substance solutions such as mono‑PP, -HDPE or -PET, we advise independently of manufacturers, which film qualities would be suitable for your specific requirements.
“Sustainability is a strategic issue for the packaging industry. More and more of our customers have recognized this and involve us in their considerations right from the start. The benefit to you? A faster approach to future safe, sustainable processes.”
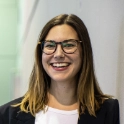
Maren Kobusch
Strategic Product Manager Smart Services & Tools
Sustainable packaging with innovative solutions
Do you need a process-safe line that will enable you to switch to recyclable, climate friendly materials and make the entire packaging process resource-efficient? With the PTC 200 Parenteral Tray Center and the BEC 400 blister line, you will be ideally positioned for future requirements.
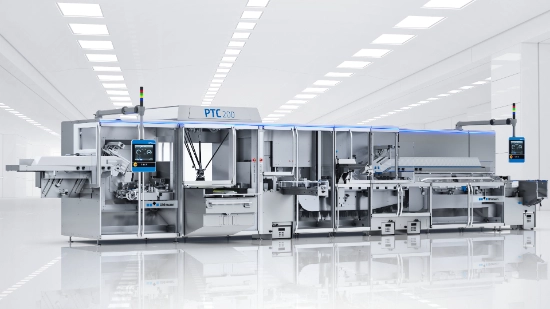
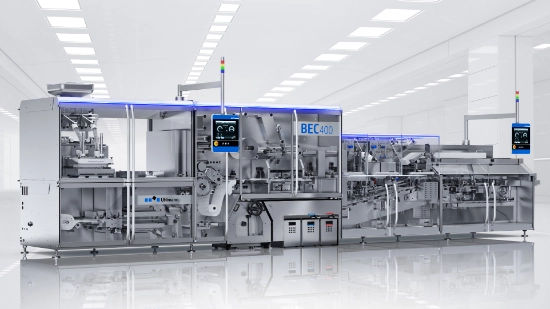