Uhlmann services – tailored and from a single source
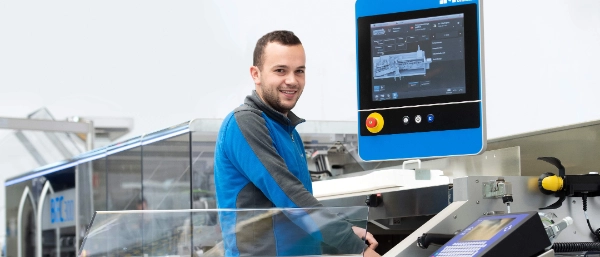
We support you in all matters to do with pharmaceutical packaging. Our experts at 17 sites across the globe are looking forward to talking to you!
We are there for you – 24/7
We not only develop reliable, powerful blister machines and packaging lines. We also ensure that you can always produce efficiently and support you with tailored services.
A spare part needs to be replaced, the control software needs to be updated or a staff shortages need to be bridged? New employees need to be trained or existing systems need to be moved? We provide flexible and solution-oriented expert support. On demand, project-related or permanent: We offer a comprehensive range of services – tailored to your individual requirements.
And of course we are there for you if there is ever a technical malfunction on your machine:
24/7 service hotline: +49 (0)7392 702 8702
Services for your individual requirements
We support you in ensuring that your machine achieves the best performance and works with maximum productivity – from the very beginning and in ongoing operation.
From ramping up your system, to ongoing operation, through to relocation – we offer advice and support you in ensuring that your Uhlmann machine runs continuously, reliably and with the best OEE (overall equipment effectiveness).
We offer the following packages:
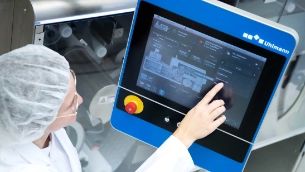
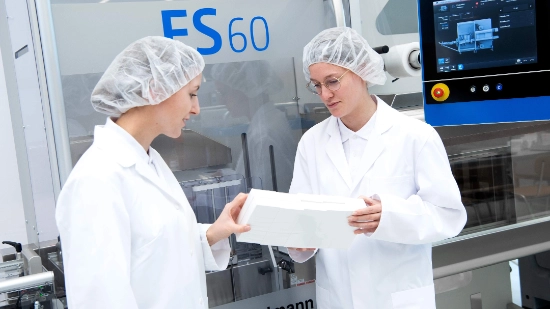
Training and qualification
A high level of machine expertise, tailored to your Uhlmann systems and lines: That is the aim of TrainingPlus.
You want to increase your team's motivation and machine expertise or efficiently train new employees on your packaging machines? From installation and operation to maintenance and administration we offer individual training plans and modules that can be freely combined for every work area.
All training courses and qualifications are divided into different levels, which can be combined and therefore tailored to each person's individual level of knowledge. Whether offered as open training sessions or as part of a comprehensive professional training program, whether held at your site, at our training center or online – our training services are always tailored to your needs. We train your employees in a long-term program with the following five modules, all of which are of course GMP-compliant.
Our training priorities for you:
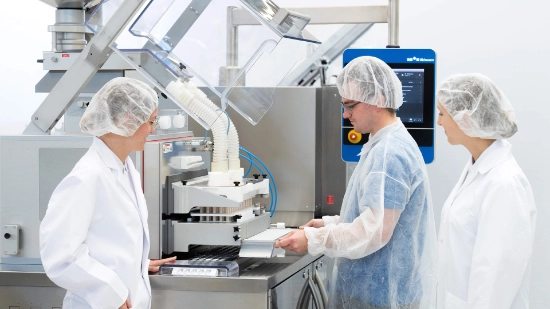
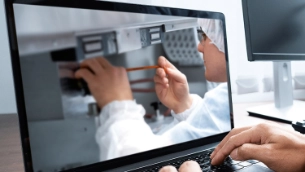
Maintenance and service
Custom system also need tailored maintenance: With our maintenance services, your machines will be perfectly serviced and keep running without downtimes in the long term. Weak points are detected in good time and the quality remains at a consistently high level. With regular inspections, you will always be one step ahead of the wear.
Benefit from our service offers for optimal maintenance planning:
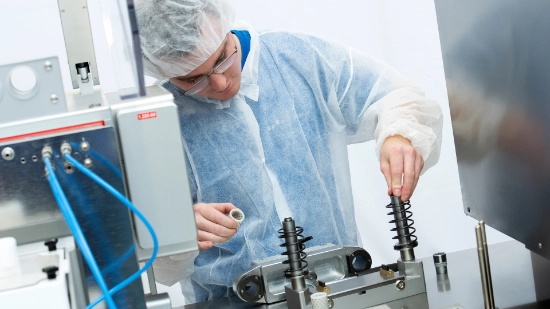
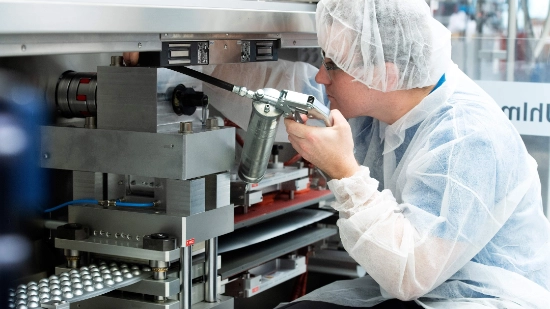
Spare parts and repairs
We are you partner for all spare parts and repairs of your packaging lines.
Our efficient team of experts, with their comprehensive specialist knowledge, knows your systems down to the smallest detail. We can identify the right components and supplement important parts even with little information. If necessary, we can pre-assemble spare parts. In an emergency, we make sure that the checked spare parts are ready to ship the same working day.
We also support you with these services:
Format parts and upgrades
Our mechanical and electrical upgrades keep your machines up to date. We adapt or replace mechanical components and make your existing systems fit for the future.
From forming tools, feedings, sealing, perforation and embossing tools to punches and format parts for transfer benefit form our unique format expertise. Our expert knowledge is the result of 70,000 standard and special tool sets and 30,000 feeding solutions for pharmaceutical customers across the globe.
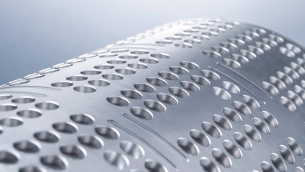
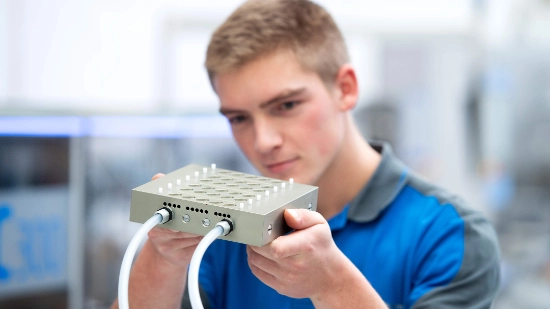