Packaging for parenteral products – challenges for the pharmaceutical industry
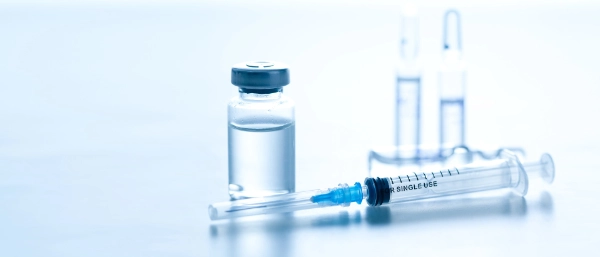
Parenteral medications are becoming increasingly important across the world – secondary packaging presents various challenges for the pharmaceutical industry.
Packaging of parenteral products – what does that mean?
Parenteral packaging refers to secondary packaging for pharmaceutical products for injection, infusion, inhalation or implantation into human or animal bodies.
Due to their ingredients also known as APIs (Active Pharmaceutical Ingredients) these medicinal products, which are already stored in primary packaging, are often temperature-sensitive. They are first packaged in a liquid or freeze-dried state in a wide range of often fragile sterile primary packagings, e.g. ampoules, vials, syringes, injectors or inhalers and are then packaged as a subsequent step with other components used for application, i.e. syringes, cannulas, adapters, pens or injectors.
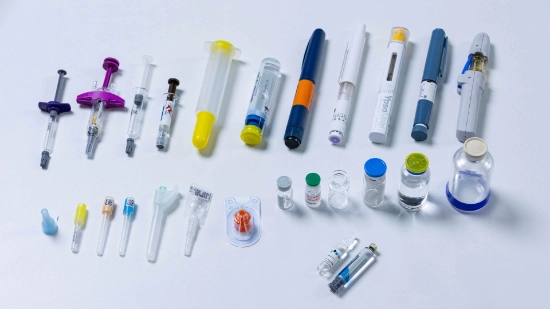
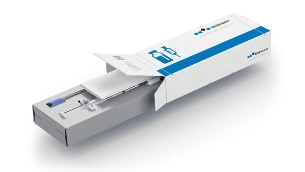
What makes the secondary packaging of parenteral products so special
Parenteral packaging is becoming increasingly important as the number of parenterally delivered medicines rises across the world examples include vaccines as well as diabetes medication and weight loss injections.
At the same time, the costs for producing parenteral products are typically higher than for oral solid dose products. Parenteral medications are often used for serious or rare illnesses, and they are sometimes personalized for specific patients. In some cases, the value of individual injectables can reach several thousand euros.
The often highly effective ingredients require special protection, e.g. against heat or light. The increased risk of breakage for the primary packaging also requires particularly careful handling. This necessitates packaging solutions that are easy to clean and then put back into operation when required.
Package parenteral products carefully and securely with Uhlmann:
Uhlmann offers a range of solutions for these requirements, ensuring comprehensive reliability and product protection, drawing on more than 75 years of experience in packaging parenteral products.
The LiPro feed solution for vials, ampoules and cartridges and the SyPro feed solution for syringes have already proven their effectiveness on numerous blister machines and the Parenteral Tray Center 200.
Assigning critical process parameters to clearly marked products not only increases the efficiency of packaging parenteral products but also ensures patient safety.
With the future-oriented Pexcite platform, Uhlmann offers a wide range of software solutions, including a Track & Trace application for clear traceability of products. Medical device tracking starts on the product level during the packaging process, ensuring maximum pharmaceutical safety in order to ensure patient protection.
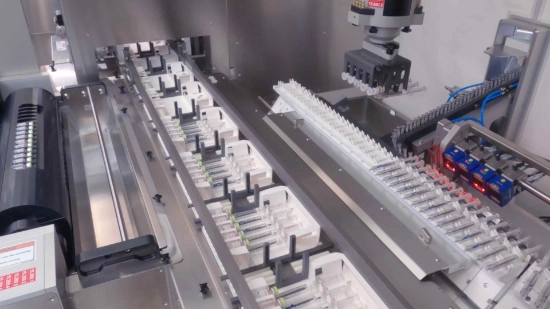
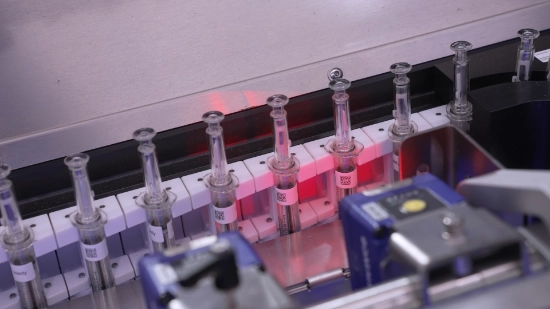
Flexibility is vital on the packaging line
From syringes, vials and cartridges to bottles, injectors and pens parenteral products in all possible shapes and sizes are found on the packaging line, often with corresponding accessories. This means that the packaging process is often a multi-stage process and the number and shape of materials to be packaged changes regularly.
In addition, different end consumers and different countries have different requirements regarding the size of batches. Batch sizes are becoming increasingly small in the high-priced sector in particular. Pharmaceutical manufacturers therefore have a strong interest in the ability to safely and above all flexibly package their products. Quick setup times when changing batches also play an important role in this regard.
Manufacturers bear a great deal of responsibility towards doctors and patients: Medications must be supplied in verifiably perfect condition. In addition, legal requirements concerning sustainability and traceability are a further factor pushing for more exacting packaging processes.
The interaction between machine technology for the right packaging solution and appropriate software tools, such as for clear traceability of medications, will become increasingly important in future.
Uhlmann stands for pharmaceutical safety and flexibility:
- Flexibility regarding products: Systems need to be able to process various different products and components and in rapid succession, e.g. ready-to-use cartridges in the morning and then vials with syringes in the afternoon. They also need to be able to follow the product life cycle of parenteral products from vials to syringes through to injectors.
- Flexibility regarding packagings: From folding cartons, plastic trays and cardboard trays to blisters, clamp packaging and paper trays the machine must be able to process all types of packagings. A wide range of inserts, such as measuring spoons, package inserts or booklets, must also be taken into account in the packaging process.
- Flexibility of packaging formats: Large, medium and small formats as well as batches smooth format change-over is particularly important here.
Parenteral Tray Center 200 – a single machine for many requirements
Meeting future requirements concerning parenteral packaging for pharmaceutical companies, medical personnel and patients will require packaging systems that can do more: Vials in cardboard trays, pens in plastic trays or indeed a product combination in secondary packaging that is as sustainable as possible – all of these are possible with the Parenteral Tray Center 200. Take the flexibility of your packaging to the next level and focus on the individual requirements of your customers.
Uhlmann packaging solutions for parenterals
Whether folding cartons, cardboard trays, blisters or clamp packaging: there is secondary packaging for every pharmaceutical product - our Packaging Competence Team will find the right solution for your individual requirements.
„The goal of product development at Uhlmann is highly flexible design of packaging solutions, ensuring that our customers can reliably and efficiently process a variety of shapes and sizes of parenteral products as well as various packaging materials and shapes.‟
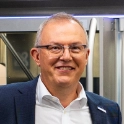
Strategic Product Manager Parenteral Packaging at Uhlmann Pac-Systeme