Preventing oxidation – packaging iron deficiency tablets
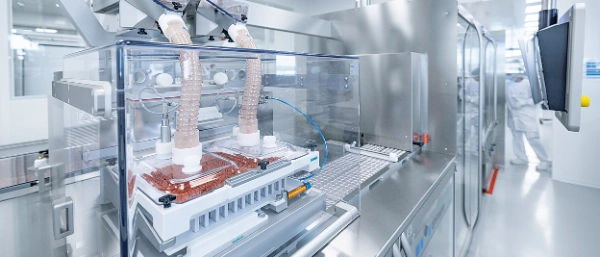
Active ingredients react with the oxygen and humidity of their environment – some more, some less. CordenPharma deals with a particularly sensitive, highly reactive product. The large tablets not only oxidize within a very short time, but also dust and break up easily. Surely a case for the pharmaceutical packaging experts at Uhlmann.
Rust never has a chance!
At CordenPharma in Fribourg (Switzerland), rust is an unavoidable part of the production and packaging processes. The Site, which CDMO acquired from Vifor Pharma in February 2022, produces oral drugs for iron deficiency and a phosphate binder in solid and liquid forms. Main ingredient: ferrous sucrose.
This particular active ingredient has its work cut out for it and poses several challenges for pharmaceutical packaging at CordenPharma: with a diameter of 18 millimeters, the tablets are not only relatively large, but also brittle and prone to dusting. Particularly sensitive product handling is necessary, as is the safe protection of the operating personnel from the dusts. In addition, all surfaces must be easy to clean. White plastic? Better not, because it would turn reddish brown in no time. Instead, glass and stainless steel are used in production.
Against this background, CordenPharma decided to invest in the expansion of its pharmaceutical packaging capacities and order two new lines from Uhlmann at the end of 2020: an IBC 150 for packaging solid products in bottles and a BEC 400 blister line.
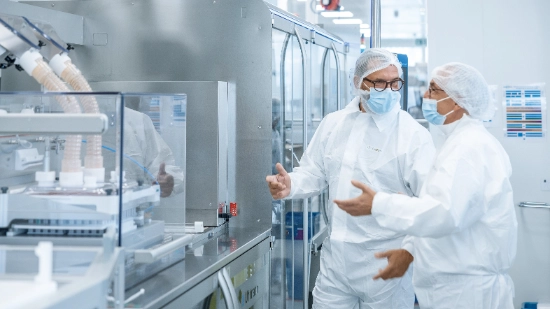
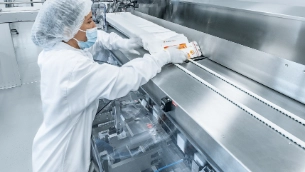
„With all the challenges during production and packaging, it’s important to remember how important preparations for iron deficiency are. More and more people – including many vegetarians and vegans – find themselves unable to absorb as much iron as they need. Demand is rising sharply around the world.‟
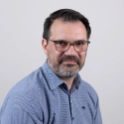
Sébastien Kunetka
Maintenance Manager at CordenPharma
State-of-the-art pharmaceutical production with rust – how can that be?
But before the lines could move in, the teams at CordenPharma and Uhlmann first had to develop an overall concept to contain dust and rust development. Today, reduced humidity and temperature prevail in the separated primary area. In addition, extensive exhaust systems were installed on both lines. To protect the operators not only from dust but also from noise, three extraction units and the cooling unit are housed in a separate technical room.
“We went for the IBC and BEC because both lines can be easily covered. The machines are also compact and spacesaving – a big plus in our cramped production site,” explains Sébastien Kunetka.
18 millimeters in diameter, brittle consistency – this calls for maximum sensitivity when it comes to handling. In order to avoid tablet breakage and to keep dust generation to a minimum right from the start, the Uhlmann experts pulled out all the stops.
For example, with the IBC 150 bottle line:
- Up to three dessicant bags are inserted per bottle – in addition to protecting against moisture, they form a cushion on the bottom of the bottle
- A tablift transports the tablets by shuttle to the two counting modules
- On the sorting plate, damaged tablets are detected and rejected by the BottleChrom camera system
- The counting modules work with low drop heights, so that tablet breakage is prevented
- A cotton ball is supplied in each bottle as transport protection
- A lid with aluminum membrane is screwed onto the bottle and the membrane is sealed via induction – perfect protection against moisture
- A retorker tightens the lid afterwards
The BEC 400 blister line is just as gentle.
Here, too, the tablets enter the SimTap 4 feeder via a tablift, which deposits the products in a targeted and low-dust manner in the pockets of the aluminum/aluminum blisters.
The VisioRead inspection system checks the presence, integrity and color of the tablets. “The iron specimens are twotone with irregular dots – a challenge for any camera. But if the system is programmed accurately, a very high level of safety can be achieved here as well,” says Roberto Zürcher.
Packaging line for solids in bottles, cartons up to the pallet
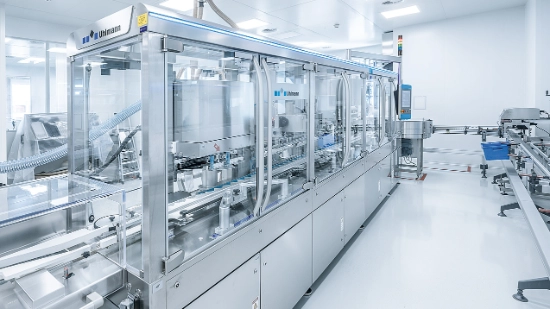
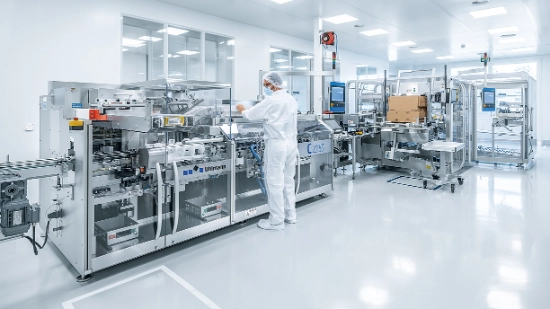
Line concept consistently implemented
The sensitive preparation is packed in airtight bottles or aluminum blisters. Where do we go from here? “It was important to us to consistently implement the line idea – from the feeder to the pallet,” emphasizes Sébastien Kunetka. Accordingly, CordenPharma, with the support of Uhlmann, set up two continuous pharmaceutical packaging lines, each networked via a control system:
IBC 150 bottle line with
- L 180 labeller for printing variable data
- C 2155 cartoner with hot glue closure
- Feeder for prefolded brochures
- ECP 12 case packer with palletizer module and two pallet positions
- Integrated Track & Trace
BEC 400 blister line with
- Blister module, SimTap feeder and preparation for pharmaceutical separation for printing variable data
- C 2155 cartoner with hotmelt closure, which can also be easily converted to a tuck-in closure
- Feeder for prefolded brochures
- ECP 12 case packer with palletizer module and two pallet positions
- Bulk discharge optionally mountable
- Integrated Track & Trace
The two lines have been in operation in Fribourg since spring 2022. “The feedback from CordenPharma has been very positive, both on the project progress and the performance of the machines. We were able to show that there is an optimal packaging process for all products – even with high requirements,” says Roberto Zürcher happily.
Packaging line for solids in blisters, cartons up to pallets with pharmaceutical separation
„To me, a good supplier is not characterized by the absence of problems, but by how they handle them. I was very impressed with Uhlmann‘s capability to solve problems and meet deadlines.‟
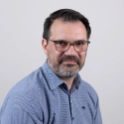
Sébastien Kunetka
Maintenance Manager at CordenPharma
Interview with Sébastien Kunetka
The Maintenance Manager at CordenPharma provides an insight into the decision-making process when purchasing new lines and why the company opted for Uhlmann.
CordenPharma International
was founded in 2006 as the global pharmaceutical services and manufacturing platform of International Chemical Investors Group, CordenPharma is a fullservice contract development and manufacturing organization (CDMO) for active ingredients, excipients, pharmaceuticals and related packaging services. At eleven cGMP-compliant sites throughout Europe and the U.S., CordenPharma’s approximately 2,600 employees turn complex processes, ideas and projects into high-quality products at every stage of development.